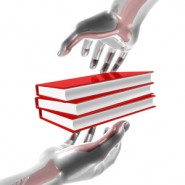
Update:
“I’ve been called the world’s most fuel-efficient chief executive,” Mr. Toyoda said.
The article below is published on November 2013 by Hiroko Tabuchi in "The New York Times". It is clearly shows how Lean transformation or Lean philosophy will make an organization in a place to recover the growth path fast an efficient. This will be a good lesson for all government, local authorities and private and public organizations.
TOKYO — In 2008, Toyota Motor was at giddy heights. Profit soared to a record high. The Japanese company knocked General Motors off its perch as the world’s largest automaker. Then an extraordinary run of bad news — the global economic crisis, a huge recall scandal and a devastating earthquake and tsunami — led Toyota’s chief executive, Akio Toyoda, to declare the company a step away from irrelevance.
After five difficult years, Toyota is picking up where it left off. The automaker said Wednesday that net income for the quarter ended in September jumped 70 percent and that it expected profit to rebound to a near-record high for its full financial year, which runs through next March, thanks to favorable exchange rates and a more streamlined cost structure.
Toyota raised its net profit forecast for the full year to 1.67 trillion yen, or $16.9 billion, up from a previous estimate of 1.48 trillion yen. The automaker — again the world’s largest by number of vehicles sold — said it expected net sales of 25 trillion yen and operating income of 2.2 trillion yen.
If Toyota meets its guidance, it will be almost back to its best year on record, which ran through March 2008, when it earned 1.72 trillion yen in net profit on sales of 26 trillion yen.
For the three months through September, net income jumped 70 percent to 438.4 billion yen, Toyota said. Sales grew 16 percent to 6.28 trillion yen. Operating profit grew almost 74 percent to 251.4 billion yen.
Nobuyori Kodaira, an executive vice president of Toyota, attributed the strong results to a weaker yen, which increases the value of the automaker’s earnings overseas. He also credited the change in fortunes to a concerted undertaking to reduce costs, both within Toyota and at its suppliers.
“Of course, the weakening of the yen worked in our favor,” Mr. Kodaira told reporters in Tokyo. “But the effort we and our partners put into driving down costs also led to this turnaround.”
Toyota shares rose 0.5 percent to 6,350 yen in Tokyo on Wednesday before the after-close earnings announcement. Shares in the automaker have climbed almost 60 percent this year, outperforming the benchmark Nikkei 225-share index, which has risen about 40 percent.
The yen has weakened by 12 percent against the dollar during the same period, thanks to an aggressive monetary easing policy by the Japanese central bank, at the urging of Prime Minister Shinzo Abe’s government.
“The cyclical and intensely competitive nature of the global automotive industry may once again spoil the picture,” Clive Wiggins and Kelly Zou, auto analysts at Macquarie, said in an Oct. 21 report on Toyota, “but there are also reasons to remain bullish on returns — namely, a renewed commitment to operating efficiency in the wake of the lean post-global financial crisis years.”
Still, Mr. Wiggins and Ms. Zou warned that a slowdown in Asia, as well as a weakening market share in the increasingly competitive United States and China, could pose risks to Toyota’s return to hefty earnings. So could a loosening in cost discipline now that profits are rolling in, they said. Toyota and other exporters have come under government pressure to raise wages to spread the benefits of a weaker yen.
Toyota is outshining its domestic rivals. Last week, Nissan slashed its profit forecast because of slowing demand in emerging markets and mounting recall costs. Honda said that sales were brisk in the United States and Japan but that its profits had been weighed down by heavy investment in new production lines.
At the heart of Toyota’s cost savings has been a strategy called the new global architecture, led by Mr. Toyoda, a scion of Toyota’s founding family. The program involves sharing the same parts across a wider range of models, and adopting standardized parts used by other global automakers. The 2015 Prius gas-electric hybrid is to be the first model fully manufactured under that new initiative.
With a return to big profits in sight, Toyota is also on the offensive again in next-generation green technology. The automaker, a pioneer in hybrid cars, said Monday that it would show a prototype hydrogen fuel-cell vehicle at the Tokyo Motor Show later this month. The four-seat sedan has a driving range of 500 kilometers, or about 300 miles, and can be refueled in minutes, according to Toyota. The automaker hopes to sell its first fuel-cell car in 2015.
During its difficult years, Toyota raised eyebrows by going all out to winnow even its executives’ pay. In the thick of the global economic crisis, Mr. Toyoda’s pay came to 116 million yen. In 2013, Mr. Toyoda got a raise to 184 million yen, according to company filings. That’s still about a tenth of what is received by Ford’s chief executive, Alan R. Mulally, including stock options.
The gap led Mr. Toyoda to joke at a talk with Japanese university students in September that Toyota’s commitment to cost cutting and efficiency went beyond its cars.
“I’ve been called the world’s most fuel-efficient chief executive,” Mr. Toyoda said.
----------------------------------------------------------------------------------------------------------------------------------------------------------------
Update: November 2013
Lean Transformation
Lean transformation is not just about new concepts and tools. It is about changing your organization's social system (i.e. culture, thinking, and behaviour). It does require extraordinary leadership and vision. It is well worth the effort and the difficult journey.
This schematic graph summarizes the road map.
----------------------------------------------------------------------------------------------------------------------------------------------------------
Update: October 2013
Local government performance indicators
Effective local government is the backbone of strong communities. It is responsible for aspects of everyday life that people care about deeply – from vibrant and safe public spaces, to well-stocked libraries, to strong local business and employment opportunities. Effective performance reporting by authorities is essential for ensuring accountability to residents and ratepayers as to how public money is being spent and the quality of services delivered. Improved performance reporting by local government has been a topic of discussion for many years and always has a new ideas.
Click here for more information.
------------------------------------------------------------------------------------------------------------------------------------------
Update: September 2013
Local Government Efficiency
Measuring performance in the private sector is straightforward. Subtract how much it costs you to make something from how much you sell it for and there's your profit. For private sector firms, profit signifies success and measuring performance can be done in tidy mathematical terms.
But what happens when your organization is "not here to make a profit"? In the public sector, money (or tax) is the cause of the work, while the desired effect is the maximization of the public good achieved through spending it. There are ways to measure municipalities services. Click here for an article showing some of it.
----------------------------------------------------------------------------------------------------------------------------------------------------------------------
Update: August 2013
Lean Models for performance improvement:
Companies are increasingly embracing lean production techniques in their efforts to improve performance.
Yet the majority of these companies fail to tap the full potential of “going lean.”
Click here for a presentation to show how lean models can help to improve and increase performance.
------------------------------------------------------------------------------------------------------------------------------------------------------------------------
Update: July 2013
Green Production
Green Production is an organizational strategy that focuses on profitability through using environmentally friendly operating processes. The prime purpose of Green Production is to reduce environmental impact of manufacturing process at every stage and have three fundamental objectives:
- Decrease emissions, hazards, effluents, and accidents;
- Minimize the life cycle cost of products or/and services;
- Reduce of raw materials and non-renewable forms of energy.
When this subject incorporates with Lean manufacturing we can see how Lean will be applied:
Here is the link of more information on this subject.
------------------------------------------------------------------------------------------------------------------------------------------------------------------------
Update: June 2013
Morning market
A daily routine at gemba that involved examining rejects made the previous day before the work begins so that countermeasures can be adopted as soon as possible, based on gemba-gembutsu principles.
Click here for a good discussion on this subject.
------------------------------------------------------------------------------------------------------------------------------------------------------------------------
Update: May 2013
Lean culture
Lean is a business methodology of continuous improvement, based on the Toyota Production System (TPS). Companies that attempt lean management find that lean methodologies are not transformable by themselves. The methodologies are sound, but for lean to work, employees must believe it is how they should do business on a daily basis.
Click here for the definition of lean culture.
------------------------------------------------------------------------------------------------------------------------------------------------------------------------
Update: April 2013
Lean Thinking
Lean thinking is a highly evolved method of managing an organization to improve the productivity, efficiency and quality of its products or services. Japanese and American management specialists developed the ideas and methods over the latter half of the last century. These management techniques have been employed both in the aerospace industry (Boeing) and in the auto sector (Toyota). In the manufacturing sector, the concept is sometimes referred to as World Class manufacturing or High Performance Manufacturing.
Here is the link for the Book Review: Lean Thinking by Womack and Jones. Prepared by. Annalisa L. Weigel
------------------------------------------------------------------------------------------------------------------------------------------------------------------------
Update: March 2013
Visual management is used to show how we are managing and measuring our business. Visual Management is certainly one of the characteristic traits that set lean organizations apart from all others. The success of Visual Management is predicated on relevant and current data. To be effective, Visual Management must be embraced and utilized by leadership, management, and employees throughout the organization. Any process has inputs that can be controlled using visual management.
The outputs can display performance, method, layout and status of a production cell in a clear, simple visual form. The following link is a sample of how this idea works in lean organizations.
Visual Management Lean Ergonomics - A successful implementation within a Kizen Event
------------------------------------------------------------------------------------------------------------------------------------------------------------------------
Update: February 2013
Considering launching an ergonomics initiative that’s integrated into your Lean Manufacturing and Six Sigma improvement processes?
Over the past few decades, several corporate improvement initiatives or programs have been developed to aid corporations in achieving external productivity excellence, most notably Lean Manufacturing and Six Sigma. Our experts lead this discussion on the proven strategies, tools, and techniques necessary to build a successful and sustainable ergonomics program that combines Lean Manufacturing and Six Sigma methodologies while also achieving bottom-line results.
Optimizing human performance, reducing cycle time, and implementing measurable business processes, all serve to increase your support organization’s agility, responsiveness, and ability to deliver enhanced services. By integrating theses methodologies, your organization becomes a stronger business partner to all stakeholders by providing:
- Increased cost competitiveness;
- Lower per transaction costs;
- Empowered, customer and process-focused workforce; and
- Dedicated commitment to continual improvement.
Click here for more information look for the following research link from Institute of Industrial Engineers.
------------------------------------------------------------------------------------------------------------------------------------------------------------------------
Update: January 2013
Merry Christmas and Happy New Year!
After we got a few feed backs from our web users, we are going to add new words to our website Glossary.
These new words are:
Gemba:
Workplace. Five rules of golden rules of gemba management are: (1) Go to gemba, (2) check gembutsu, (3) take temporary measures on the problems, (4) find and eliminate root cause (5) and finally standardize to prevent recurrence.
Housekeeping:
Introducing good housekeeping in gemba reduces the failure by 50 percent, and standardization further reduces the failure rate by 50 percent of new figure.
Standardization:
Ref. to Housekeeping
Five M’s (5M):
A method for managing resources in gemba. Specifically those known as “5M” Manpower, Machine, Material, Method, and Measurement.
Gembutsu:
The tangible objects found at gemba such as work pieces, rejects, jigs and tools, and machines.
Hiyari KYT (kiken-yochi training):
Hiyari KYT refers to the practice of anticipating danger in advance and taking steps to avoid it.
Hiyari Report (scare report):
Hiyari Report (the scare report) is a written form from a worker to a supervisor that reports a condition that is unsafe and could lead to quality problems and/or accident.
Ishikawa (fishbone) diagram:
A diagram originally developed by professor Kaoru Ishikawa to show causes (process) and the effect (result). The diagram is used to determine the real cause(s) and is one of the seven basic tools of problem solving
Jidhoka (autonomation):
A device that stops the machine whenever the defective product is produces. This device is essential in introducing JIT.
JK (jisho kanri):
Jisho kanri means autonomous management in Japanese and refers to workers’ participation in kaizen activities as part of their daily activities under the guidance of the line manager. It is different from Quality Circle activities which are voluntary and are carried out by the workers’ own volition.
Kaizen concepts:
Major concepts that must be understood and practiced in implementing kaizen are as following:
(1) Kaizen and management, (2) Process versus result, (3) following the PDCA/SDCA (4) putting quality first, (5) speaking with data, (6) treating the next process as customer
Kaizen story:
A standardized problem-solving procedure to be used at each level of organization. Kaizen story has eight steps: (1) select a project, (2) understand current situations and set objectives, (3) analyze data to identify root causes, (4) establish countermeasures, (5) implement countermeasures (6) confirm the effect (7) standardize, and (8) review the above process and work on the next steps.
Kaizen systems:
Major systems that must be established to attain a world class status are:
(1) Total Quality Control (Total Quality Management), (2) Just-In-Time (JIT) production system, (3) Total Productive maintenance, (4) Policy deployment, (5) Suggestion system, and (6) Small-group activities.
Kosu:
Manufacturing operations can be divided between machine hours and man hours. Kosu refers to the specific man hours it takes to process one unit of a product in a given process and is calculated by multiplying the number of workers involved in a process by the actual time it takes to complete the process, and dividing that by the units produced. It is used as a measure of operators’ productivity. Kosu reduction is of the key measures of productivity improvement in gemba.
Morning market:
A daily routine at gemba that involves examining rejects (gembustu) made the previous day before the work begins so that countermeasures can be adapted as soon as possible, based on gemba-gembutsu principles. This meeting involving the gemba people (and not staff) in held first thing in the morning.
Mura:
Japanese word meaning irregularity or variability.
Muri:
Japanese word meaning strain or difficulty.
------------------------------------------------------------------------------------------------------------------------------------------------------------------------
Flexible Approaches to Implementing Lean Manufacturing
Running your company as efficiently as possible has become critical in recent years and even more urgent during the struggles of today´s economy. Some alternative approaches are beginning to help companies implement Lean Manufacturing improvements quickly, inexpensively, and without overburdening staff resources.
This article will briefly describe four new approaches being pioneered in an effort to make Lean implementation available to all companies regardless of their financial situation or personnel constraints. No matter what approach you take to becoming Lean, allow yourself and your staff to enjoy the process. Few events in manufacturing are as exciting or dramatic as radically improving your workplace and the camaraderie of good people eagerly engaged in making the company better and stronger for everyone. Focus any of the programs described below at your company´s "constraints" and you will increase throughput and profits while substantially reducing waste.
Lean On the Run: Perhaps one of the most innovative approaches to implementing Lean quickly and with minimal downtime, Lean On the Run uses the experience and talents of a Lean Consultant/Facilitator, an assistant, and occasional help from the "team" or staff assigned to the area being improved.
In practical terms, an important area of business functioning is selected for rapid improvement to achieve defined goals and objectives. The "team" participates in a brief but convincing training session and demonstration of Lean principles, after which they are released to the shop floor to begin work as usual. The facilitator and assistant then get very busy progressing through a discovery process examining the target area and every aspect of its functioning. The pair carefully observes, learns the process, and solicits input from the operators/staff to acquire needed data. You might say the facilitator and assistant function something like a computer´s "CPU" gathering data, processing it, and then providing output for decision-making.
Periodically, the team is "huddled" together to discuss observations, try out new methods, and make operational/functional decisions. When the team and management agree upon a clear vision of improvements needed, a plan is developed to implement the improvements at the earliest opportunity.
Normally, full implementation will require an 8-10 hr. commitment spread over a week´s time, for 6-10 people. This is less than 20% of the usual time needed for standard "Kaizen Events" or "Blitzes." Downtime is kept to a minimum by making major changes during off-shifts, temporarily building additional inventory to offset any interruptions, and other effective strategies. This approach works particularly well when companies have reduced staff or are simply too busy to slow or shut down production for extended periods.
OJT Lean: Most states now have funds available to help companies upgrade the skills of their workforce through "Custom Fit" and OJT (On-The-Job Training) programs. These funds are typically used to "invest" in local companies for the collateral benefits gained for local and state economic development. The focus is less "team" based and more dependent on the trainer/trainee(s) relationship and their engagement in applying improvement activities throughout the company. Implementing Lean Manufacturing techniques throughout the company while transferring "Lean Expertise" to the in-house "Improvement Manager" trainee(s) is the goal of this program. Hours of instruction are conducted in a primarily hands-on fashion as the Lean expert teaches, coaches, and collaboratively implements various aspects of Lean Manufacturing throughout the company. Trainees are given improvement assignments and are mentored through this process in an intensive four to six month undertaking that makes Lean experts out of existing staff. This approach eliminates the need for increasing head-count, implements the majority of the "big bang" Lean techniques, and insures deep level understanding and capabilities of the trainee(s). After the training period, the expert level "Improvement Manager(s)" guides the company through new improvement initiatives as needed without further outside support.
Lean Right Now: This is a typical "Kaizen Event" or "Improvement Blitz" approach with a few twists. The "Lean Right Now" approach exemplifies engaging in the implementation of real improvements with a diverse team made up of committed individuals from throughout the company to affect significant change very quickly. Emphasis is placed on strategic, tactical employment of Lean tools that increase throughput and reduce waste almost immediately. "Analysis Paralysis," or overanalyzing issues to the point that nothing actually gets done is avoided by using this methodology. Typically, this approach will require the full-time efforts of 6-10 people for five days to achieve full implementation in a single area or concern. When creatively engaged and empowered, "Blitz Teams" routinely achieve incredible results using this approach. It is among the more costly programs with regards to committed staff resources, but typically results in some of the largest improvements and greatest team buy-in. Team buy-in, commitment, and empowerment ensure long-term effective improvement activities. If you have the ability to commit 6-10 people to this process for a week it is among the most powerful approaches to implementing Lean available.
Walkabout Lean: From the "land down under" the term "walkabout" refers to someone taking a long walk, exploring, taking a look around, etc. That is the beginning of this approach to implementing Lean. A Lean expert carefully looks over the production facility along with a very knowledgeable in-house plant expert, noting where urgent attention is most needed. Improvement opportunities are prioritized to the company´s critical success factors and plans are laid to systematically address the improvements promising the greatest impact sequentially. Operators are observed and asked for regular input and occasionally some help, but are mostly left to their jobs. Using available personnel from focus areas and throughout the company, major improvements are accomplished in a very flexible and fluid process. This technique is most useful when staffing is tight, or production is unable to slowdown during the improvement process. A skilled facilitator can make this a "team process" by carefully listening to and incorporating input from area operators. Generally, however, this approach will not initially increase the "team buy-in" that other approaches foster. On a serious budget of time or staff this approach can deliver fast and powerful results with little disruption. Don´t let the quirky name for this approach fool you, when you turn an improvement expert lose in your plant exciting and important changes will not be far behind.
Using these streamlined approaches to becoming Lean very quickly and inexpensively will help companies become stronger and more profitable with unprecedented speed over more conventional implementation programs. To be very realistic, dramatic improvements are exiting, but creating a culture that embraces and sustains Lean processes as well as implementing Lean throughout an entire company is a long-term endeavor. It should also be noted that becoming Lean is only part of the equation. Developing your staff with cross-training opportunities and validating their input on company issues, etc., will yield benefits such as innovation and loyalty for years to come. Furthermore, don´t forget to have fun with your transition to Lean Manufacturing. Sure, some of the obstacles will be formidable, but the improvement process is generally very exciting and rewarding for all involved.
------------------------------------------------------------------------------------------------------------------------------------------------------------------------
Update: November 2012
Lean Thinking and Agile Methodologies
Several conversations in context of Lean and Agile have revealed a few patterns that we would like to share. Some people talk about Lean and Agile as if they are the same things, some try to distinguish as if they are not, and some are simply caught between the two, not sure what is what. Another observation - a lot of folks in their conversations use Lean and Agile and almost come across unsure about what they exactly are.
We have heard them all - agile way, agile manner, agile methods, agile practices, agile processes, agile framework, agile tools, and a few more.
What's the difference? Let's see if the two bullet items below start to draw a picture:
- Lean Thinking and Agile Methodologies
- Lean Principles and Agile Practices
Basically, Lean is a philosophy and Agile is a set of practices. In not so refined and all encompassing manner , the philosophy is to avoid the waste which can be implemented using some practices. That's the difference.
Click here for the PPT of this subject
------------------------------------------------------------------------------------------------------------------------------------------------------------------------
Update: October 2012
Industrial Engineer's quarterly column about lean manufacturing (May 2012)
Live lean or die
We have heard the statistics. “Small businesses represent 99.7 percent of all employer firms, employ half of all private sector employees, pay 44 percent of total U.S. private payroll, generated 65 percent of net new jobs over the past 17 years, create more than half of the nonfarm private GDP, hire 43 percent of high-tech workers (scientists, engineers, computer programmers, and others), … make up 97.5 percent of all identified exporters and produced 31 percent of export value in FY 2008 [and] produce 13 times more patents per employee than large patenting firms,” according to the Small Business Administration.
In short, small businesses drive the U.S. economy.
Explanations vary, but one common theme is the longstanding belief that small businesses “tend to be more nimble, more creative [and] less bound up in bureaucratic rigamarole,” Kathleen Melymuka wrote in CIO magazine. In the parlance of industrial engineering, small businesses tend to be more lean.
Small business owners should be familiar with lean because practicing lean principles will keep their organizations alive, according to business systems coach Ron Carroll. Indeed, this Darwinan imperative is the missing ingredient in many unsuccessful lean implementations.
Yet most practitioners of industrial engineering and lean methodologies occupy organizations of scale. The father of industrial engineering, Frederick Taylor, spent the balance of his career working and consulting in large factories. And the business most associated with lean manufacturing, Toyota, was a huge company before it embraced lean precepts. In a sense, we use lean principles to help transform a large organization into a small one.
Lean orthodoxy argues that leadership involvement is the secret sauce of success. And while it is true that “leadership teams can jump-start the culture change process by issuing organizational behavioral expectations … and behavioral expectations will only produce culture change if they are modeled by the leadership team,” according to WCM Associates LLC President Larry Rubrich, successful lean needs much more.
Certainly, leadership commitment is critical. Mission statements on the backs of employee badges or a company meeting to announce a re-org are not sufficient. If lean implementation becomes what Richard Kallage calls “Let’s give it a try” instead of “We will do it, and here’s why,” failure often follows.
For instance, you must have a compelling vision of the company’s future. Without this vision, it’s hard for top management to develop the passion and determination needed to implement lean, Kallage wrote for Thefabricator.com. Without the passion, the initiative likely will flounder. Yet for leadership team members to instill this sense of purpose and dedication they, in turn, need to be highly motivated. The moment that leadership teammates realize that failure is an option, they will revert.
So where does this leave us? Managing a large organization often has been compared to steering a large ship, but lean often is like whitewater rafting. Without inventory to buffer the ride, each jagged rock in the river becomes a life-threatening obstacle. And given a choice, the rational individual usually will opt for passage on the slow-moving ship over the hair-raising raft. Even if the ship is the Titanic. Often, organizational inertia is just too strong.
So the challenge for the lean practitioner is to do more than set up work teams or model the precepts of lean thinking; rather, your challenge is to sell, starting at the top, the notion that lean is not just an option, an alternate business model or another re-org, but rather an organizational imperative. Perhaps the motto should be: Live Lean Or Die.
Paul Templin is a materials engineer and supply chain professional with a multinational consumer electronics company. He can be reached at dstemplin2@juno.com.
Update: September 2012
QFD is a quality approach to new product design, development, and implementation driven by customer needs and values. QFD has been successfully used by many world class organizations in automobiles, ship building, electronics, aerospace, utilities, leisure and entertainment, financial, software, and other industries.
------------------------------------------------------------------------------------------------------------------------------------------------------------------------
Update: August 2012
Hosin or Hoshin Planning (HP)
Also known as Management by Policy or Strategy Deployment. A means by which goals are established and measures are created to ensure progress toward those goals. HP keeps activities at all levels of the company aligned with its overarching strategic plans. HP typically begins with the “visioning process” which addresses the key questions: Where do you want to be in the future? How do want to get there? When do you want to achieve your goal? Who will be involved in achieving these goals? HP then systematically explores the ‘what’s, ‘who’s and ‘how’s throughout the entire organization.
------------------------------------------------------------------------------------------------------------------------------------------------------------------------
Update: July 2012
Lean Thinking and JIT (Lean tools)
Lean thinking is a means of looking at how you create value that your customers truly desire with the minimum resources.
It can be applied in any industry but common applications include:
- Manufacturing
- Office
- Health Care
- Product Development
Generic Tools that can be applied in lean thinking include:
- 5S
- Value Stream Mapping
- Single Minute Exchange of Dies (SMED)
- Just in Time (JIT)
- Waste Analysis
- Problem Solving
- Teamwork
- Visual Performance Measurement
We at H4M Lean Consulting Group, consider 5S and Visual Controls to be the foundation of Lean Manufacturing systems. 5S and Visual Controls are workplace organizational tools that provide the necessary groundwork for workplace improvement. 5S and Visual Controls ensure that there is a place for everything and that everything is in its place—clean and ready to use.
Lean Consulting , 5S and Visual control
A value stream map (VSM) is a drawing that depicts the flow of material and information along a value stream (the linked series of processes that brings a product from raw materials into the hands of the customer, or that provide a service to a customer).
A value stream map is generally hand drawn, as it lets the mapper record information on the spot. For that reason, a value stream map often looks a little scruffy from traveling around the company.
Many people will copy a value stream map into a graphics program, such as Microsoft Visio, which has a value stream map stencil pack.
The Basics of Value Stream Mapping (VSM)
Heijunka (production levelling) is Japanese technique of achieving even output flow by coordinated sequencing of verysmall production batches throughout the manufacturing line in a lean production or just in time (JIT) System.
Click here to watch a PowerPoint presentation which has valuable points on this technique.
------------------------------------------------------------------------------------------------------------------------------------------------------------------------
Update: June 2012
Kaizen Blitz
Kaizen Event Best Practices - Institute of Industrial Engineers
Andon Board: Japanese name for a visual production-control device
This control device (usually a lighted overhead display) continuously shows changing status of the production line and sounds alerts if a problem is imminent.
Click here to watch a PowerPoint presentation with samples of how to use this board.
------------------------------------------------------------------------------------------------------------------------------------------------------------------------
Update: May 2012
Single Minute Exchange of Die (SMED)
A Strategy for Performance Excellence
Lean Thinking
by James P. Womack and Daniel T. Jones
Read review
Lean Transformation: How to Change Your Business into a Lean Enterprise
by Bruce A. Henderson and Jorge L. Larco (foreword by James P. Womack)
Simple Excellence: Organizing and Aligning the Management Team in a Lean Transformation
by Adam Zak and Bill Waddell
Leading the Lean Enterprise Transformation
by George Koenigsaecker
Read review
The Lean Manager
by Michael Balle and Freddy Balle
The Going Lean Fieldbook: A Practical Guide to Lean Transformation and Sustainable Success
by Stephen A. Ruffa
Tools and Techniques for Advanced Manufacturing
------------------------------------------------------------------------------------------------------------------------------------------------------------------------
Update: April 2012
Lean Thinking Videos
Where Great Companies Start - Toyota: Lean Thinking
Where Great Companies Start - Toyota: Achieving Leadership Through Integration
Where Great Companies Start - Toyota: The Essence of Leadership
Toyota: Minimizing misses for operational excellence
Introduction to Lean Six Sigma Methods
Did we leave something out? Please don't hesitate to contact us with additions to the list.